
Industry 4.0 and Shifting Shop Floor Undercurrents in India

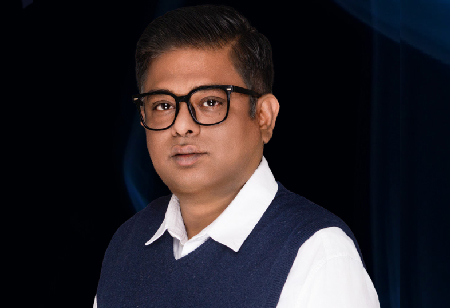
Dr Arunkumar Subramanian, CSO, Finern Automation International, 0
As the digital transformation in the global manufacturing industry is entering its fine-tuning phase, India is betting huge on manufacturing. Finance Minister Nirmala Sitharaman recently stated that India plans to increase the share of the manufacturing sector from 12 percent to 23 percent over the next two decades, aiming to create jobs and drive economic growth. It’s imperative that the industry embrace Industry 4.0 wholeheartedly to achieve its full potential. According to a report by IMARC Group, the Industry 4.0 market in the country is projected to reach $17.4 billion by 2033, growing at a CAGR of 12.40 percent. Sharing pragmatic insights of navigating the technological transformation across the manufacturing shopfloor through an exclusive interview with CEO Insights is Dr Arunkumar Subramanian, Chief Strategy Officer of Finern Automation International.
In shopfloor terms, where are we currently regarding Industry 4.0?
It’s true that many manufacturers still rely on manual assembly or operators to run their factories, which presents inefficiencies. Today, it is crucial for a manufacturing company to develop comprehensive machine programs that enhance productivity and automation. For instance, a key component of our systems is the Manufacturing Execution System (MES), which provides real-time data from our machines. As the machines operate, the MES captures critical metrics such as production rates per hour, operator involvement, machine output, yield, downtime, reasons for stoppages, and overall productivity balance. This information is invaluable for management, production teams, and maintenance personnel, allowing them to make informed decisions and react immediately to any disruptions.
By integrating MES, we enable seamless access to live production data via mobile devices, ensuring stakeholders at all levels can monitor operations remotely and respond proactively. Whether it's identifying bottlenecks, addressing machine failures, or optimizing workflow efficiency, our MES-driven automation empowers manufacturers to maintain peak performance and improve overall productivity. This is just one of the many ways we contribute to the advancements of Industry 4.0 in manufacturing.
What are the key areas where technologies like IoT, Artificial Intelligence, and Robotics drive tangible advancements?
Let’s take the case of Industrial IoT (IIoT). Our machines operate continuously, and we strategically integrate sensors to monitor wear and tear in critical components. These sensors detect potential failures, such as a belt nearing the end of its lifespan after six months of uninterrupted operation, and alert teams to prepare replacements in advance. This minimizes downtime, allowing for short, planned stoppages instead of unexpected failures, ultimately enhancing productivity.
Beyond predictive maintenance, preventive maintenance is equally crucial. Since machine components vary in lifespan, AI-driven information systems track their usage, ensuring timely interventions to prevent breakdowns and extend operational efficiency. Additionally, robotic integration is transforming flexibility in manufacturing. Traditionally, machines require complete reconfiguration for new products, but six-axis and flexible robots enable seamless modifications without extensive redesigns, significantly reducing capital expenditures.
AI and deep learning algorithms also optimize quality control. Our systems, equipped with intelligent cameras, continuously assess product integrity in real-time, identifying unpredictable variables and alerting operators to corrective actions. This in-process quality monitoring eliminates reliance on periodic sampling, ensuring consistency and reliability while driving efficiency in high-volume production environments. These advancements define the next level of industrial automation.
What are the kind of tangible benefits we are talking about?
Over the past five years, we have saved approximately £80 million in production costs by implementing deep learning systems to enhance in-process quality control.
Our software and algorithms continuously learn and improve over time, leading to progressively higher accuracy and efficiency. When we first introduced automation, the initial quality yield was around 85 percent. However, as the system adapted and optimized its processes, the yield steadily increased to 95 percent, eventually reaching an impressive 99.5 percent at its peak. With continuous innovation in AI, robotics, and automation technologies, the industry will only continue to evolve, unlocking new possibilities for streamlined production and cost savings.
These transformations have also influenced changes in the role of a Chief Strategy Officer (CSO). How do you perceive your role today?
Strategy has long been a cornerstone of business, evolving from simple planning to a critical organizational function. Traditionally, a CEO or planning manager handled strategic oversight, but as businesses grow in complexity, dedicated roles like CSO become essential. A strategist must analyze macroeconomic trends, social and political dynamics, and industry shifts to anticipate future challenges and opportunities.
My role extends beyond observation; I actively shape the company’s long-term vision, ensuring alignment across departments. While executives focus on day-to-day operations—finance, HR, production—I integrate these efforts into a unified mission. A strategist must possess the authority to challenge deviations, reinforcing organizational focus.
Unlike conventional CSOs, I collaborate closely with the CEO rather than merely reporting to them. I identify strategic investments, expansion opportunities, and technological advancements, preparing the company for the future. Some innovations may not yet exist, but it is my responsibility to ensure we are ready. Change is often met with resistance, and part of my role is to guide teams in adapting behaviors and processes to align with our goals. The strategist serves as a visionary, bridging ambition and execution, ensuring the organization remains agile, forward-thinking, and prepared for sustainable success.
The future also depends on integrating the GenZ workforce to the fold. How has this endeavor been so far?
Generation Z has grown up with digital technologies being a part of their life, shaping a unique approach to work and problem-solving. Unlike previous generations who built their understanding from foundational principles, Gen Z starts midstream, leveraging existing technologies rather than reconstructing from the ground up. While this may seem unconventional, it enables them to grasp artificial intelligence and future advancements with remarkable speed. However, they face an information overload, often struggling to filter relevant insights from the vast digital landscape.
In the workplace, Gen Z expects clear communication and structured guidance. Unlike earlier generations who thrived on exploratory learning, they seek direct instructions and defined pathways. However, despite generational differences, integration is manageable, as older professionals remain adaptable. As Generation Alpha emerges with potentially even greater digital fluency, industries will continue evolving to accommodate new expectations. Business exists to serve people, and as their needs shift, organizations will naturally adjust, ensuring sustained relevance in the future landscape.
What are your thoughts on the future of automation in the manufacturing industry?
Automation has become a necessity rather than an option, fundamentally shaping the future of manufacturing. With labor availability shrinking and skill gaps widening, traditional manual work is no longer sustainable. A decade ago, skilled workers in regions like China could efficiently assemble products with precision, but today, fewer people are entering factories, making automation essential.
Also Read: Mary Barra: Icon Who Carved Woman Leadership Path in the Auto Industry
Without automation, manufacturers risk obsolescence. Customers demand efficiency and consistency, preferring automated production for its reliability. As technological advancements accelerate, automation is becoming the standard, and any company resisting this shift will struggle to compete. The future of manufacturing is fully automated, minimizing human intervention wherever unnecessary. Organizations must embrace this transformation to remain relevant and ensure long-term success.
These transformations have also influenced changes in the role of a Chief Strategy Officer (CSO). How do you perceive your role today?
Strategy has long been a cornerstone of business, evolving from simple planning to a critical organizational function. Traditionally, a CEO or planning manager handled strategic oversight, but as businesses grow in complexity, dedicated roles like CSO become essential. A strategist must analyze macroeconomic trends, social and political dynamics, and industry shifts to anticipate future challenges and opportunities.
Automation has become a necessity rather than an option, fundamentally shaping the future of manufacturing.
My role extends beyond observation; I actively shape the company’s long-term vision, ensuring alignment across departments. While executives focus on day-to-day operations—finance, HR, production—I integrate these efforts into a unified mission. A strategist must possess the authority to challenge deviations, reinforcing organizational focus.
Unlike conventional CSOs, I collaborate closely with the CEO rather than merely reporting to them. I identify strategic investments, expansion opportunities, and technological advancements, preparing the company for the future. Some innovations may not yet exist, but it is my responsibility to ensure we are ready. Change is often met with resistance, and part of my role is to guide teams in adapting behaviors and processes to align with our goals. The strategist serves as a visionary, bridging ambition and execution, ensuring the organization remains agile, forward-thinking, and prepared for sustainable success.
The future also depends on integrating the GenZ workforce to the fold. How has this endeavor been so far?
Generation Z has grown up with digital technologies being a part of their life, shaping a unique approach to work and problem-solving. Unlike previous generations who built their understanding from foundational principles, Gen Z starts midstream, leveraging existing technologies rather than reconstructing from the ground up. While this may seem unconventional, it enables them to grasp artificial intelligence and future advancements with remarkable speed. However, they face an information overload, often struggling to filter relevant insights from the vast digital landscape.
In the workplace, Gen Z expects clear communication and structured guidance. Unlike earlier generations who thrived on exploratory learning, they seek direct instructions and defined pathways. However, despite generational differences, integration is manageable, as older professionals remain adaptable. As Generation Alpha emerges with potentially even greater digital fluency, industries will continue evolving to accommodate new expectations. Business exists to serve people, and as their needs shift, organizations will naturally adjust, ensuring sustained relevance in the future landscape.
What are your thoughts on the future of automation in the manufacturing industry?
Automation has become a necessity rather than an option, fundamentally shaping the future of manufacturing. With labor availability shrinking and skill gaps widening, traditional manual work is no longer sustainable. A decade ago, skilled workers in regions like China could efficiently assemble products with precision, but today, fewer people are entering factories, making automation essential.
Also Read: Mary Barra: Icon Who Carved Woman Leadership Path in the Auto Industry
Without automation, manufacturers risk obsolescence. Customers demand efficiency and consistency, preferring automated production for its reliability. As technological advancements accelerate, automation is becoming the standard, and any company resisting this shift will struggle to compete. The future of manufacturing is fully automated, minimizing human intervention wherever unnecessary. Organizations must embrace this transformation to remain relevant and ensure long-term success.